In our Automotive Plastics Circularity pilot project, we are working to optimize plastic recycling from end-of-life vehicles during the disassembly process, gaining access to specific polymer feedstocks for the chemical industry to increase closed-loop recycled plastics.
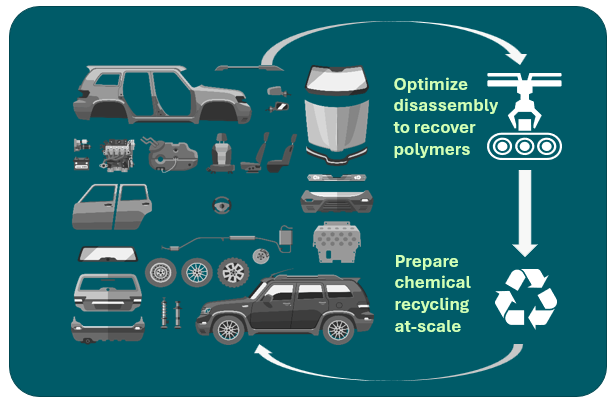
Cars are not designed for circularity. While vehicles have overall high recycling rates, the focus is on recovering and recycling metals, batteries and other high-value electronic parts. Plastics, which are found in seats and seat covers, dashboards, bumpers, lights, and throughout the vehicle, are complicated to sort and recycle considering the wide variety of types of polymers. Today only about 20% of End-of-Life Vehicle (ELV) plastics are recycled while the rest is landfilled or incinerated.
Vehicle manufacturers (OEMs) are facing increasing regulations with targets for recycled plastics and chemical companies are looking for more recycled plastics to use as feedstock in place of virgin fossil sources. This project aims to address some of the challenges blocking further recycling from happening while meeting growing demand for recycled ELV plastics.
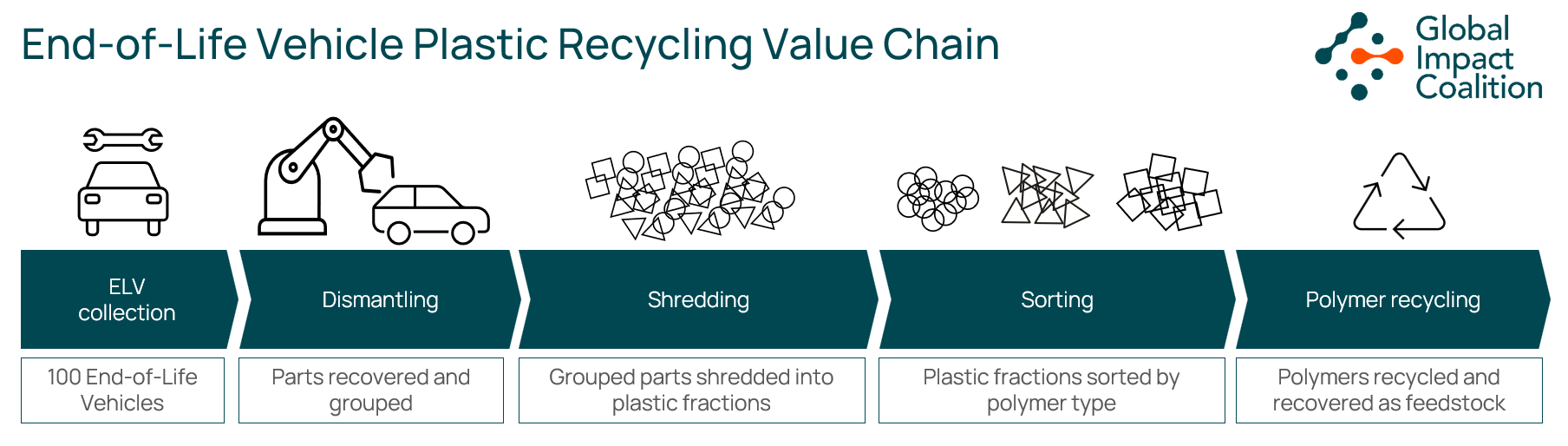
PAIN POINTS:
Current EoL treatment for cars (shredding) creates a plastic fraction that cannot be used and ends up in landfill or incineration.
UNLOCK LEVERS:
Create sufficient demand to pull out parts for dedicated recycling
Disassemblers lack knowledge to recover the right plastic fractions
Knowledge sharing through collaboration with OEMs & disassemblers
Removal of single polymers is often economically not sustainable
Creation of economies of scale by waste stream pooling and sufficient waste stream demand
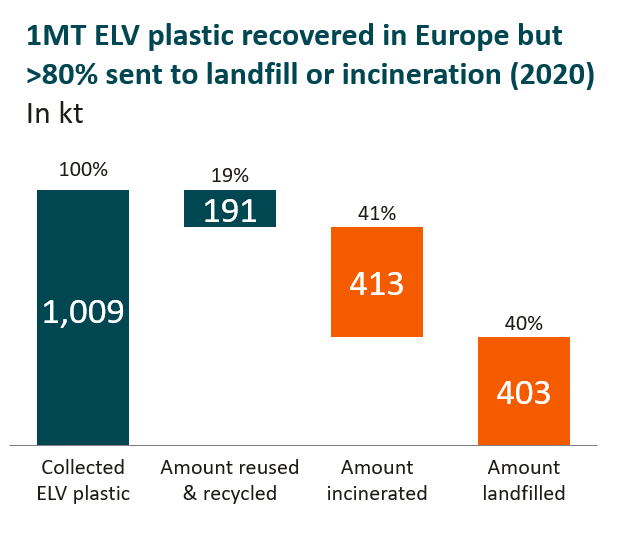
The Challenge:
Through this project, we aim to address the 800’000 metric tonnes of ELV plastic currently landfilled or incinerated each year in Europe, resulting in significant environmental and economic losses. This pilot aims to transform this waste into valuable resources, enabling automakers to meet ambitious sustainability targets for closed-loop recycled plastics.
For more information on the regulatory, economic and environmental challenges this project aims to address, see this recent article in Sustainable Plastics.